In the forest products supply chain, change is a constant. As a result, harvest schedules and operational plans must be responsive to the day-to-day changes that are occurring on the ground. By making better use of your data and resources, you can respond to any planning challenge with greater flexibility, insight and efficiency.
Let’s look at two common, real-world scenarios and how Remsoft Operations can help you respond faster, make better decisions, and save time, money and effort.
Adaptive Planning: Respond to Unexpected Events in Real-Time
Even the best plans can be pushed off track by unexpected events that temporarily halt operations. And while managing shutdowns and disruptions is always challenging, with the right information and the right tools, you can develop a plan that gets operations back on course quickly. The adaptive planning capability provided by Remsoft Operations helps planners minimize the impact of stop-work events and respond quickly and effectively to any work disruption.
The key is knowing how to respond and having technology that supports you every step of the way. Let’s take a closer look at how Remsoft Operations can help you respond to a work shutdown and resume operations after it’s over.
As a planner, when an operational shutdown is required, your first task is likely to be adjusting your harvest schedule to reflect the production gap and making sure harvesting crews stop their work until further notice.
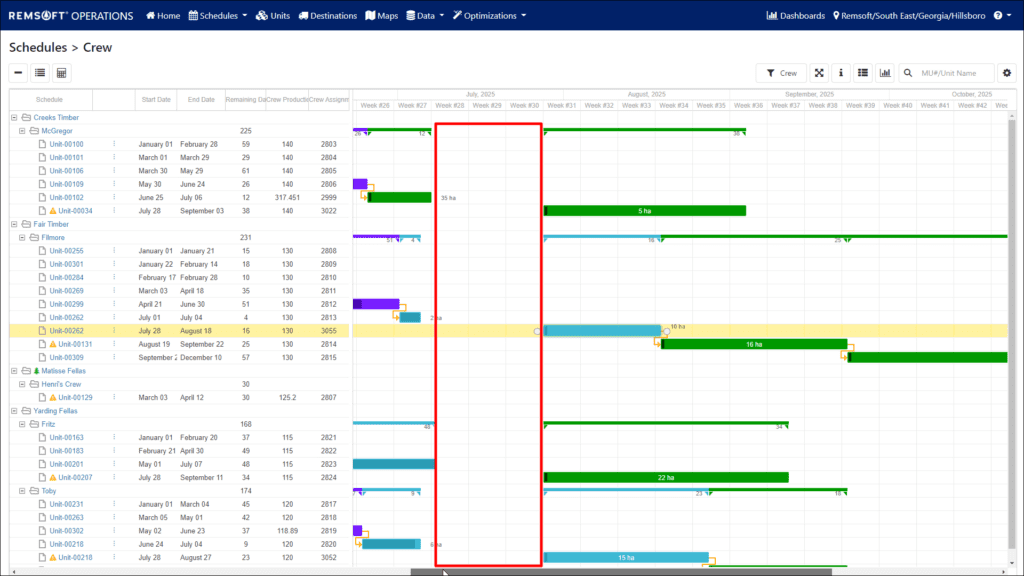
Remsoft Operations makes this easy to do. Its intuitive design allows you to stop all harvest assignments and reschedule them with the click of a button. You can also be confident that all downstream harvest actuals will be preserved and aligned once the necessary adjustments are made.
Then, it’s time to consider the ripple effects down the supply chain. With no harvesting being done, product inventories at some destinations may drop causing issues at the mill, and contracts may go unfulfilled. To address this, planner may need to find alternate units to address any shortfalls or buy product volume from the market.
With Remsoft Operations, you get a centralized view of all the data and can see the impact on each destination. The unified view of unit availability makes it easy to identify product gaps and inventory issues, and then makes it easy to schedule more units to address the shortfall or to check the market for additional products to purchase.
By moving from reactive to proactive planning, you can adapt your plans to changing conditions and keep your harvest operations running smoothly and efficiently.
Collaborative Planning: Keep Plans Moving Forward
Continuity is key in operations planning, and that’s where collaborative planning comes in. Operational and delivery plans need updating even when an area planner or other key team member is away. But staffing situations don’t have to put your plan updates on hold.
In Remsoft Operations, all data and plans are centralized, so adjusting harvest and delivery plans is a breeze for anyone on your team. With minimal remote support, authorized team members anywhere can make updates in minutes. They can view and access all the data they need to make any adjustments or updates to harvest schedules, delivery targets and crew assignments.
Now, let’s consider a hypothetical scenario: A key planner is on vacation and a valued customer in the region just asked for more pine fiber volume to be delivered in the coming months. The harvest and delivery plans need to be adjusted quickly to meet the increased volume requirement.
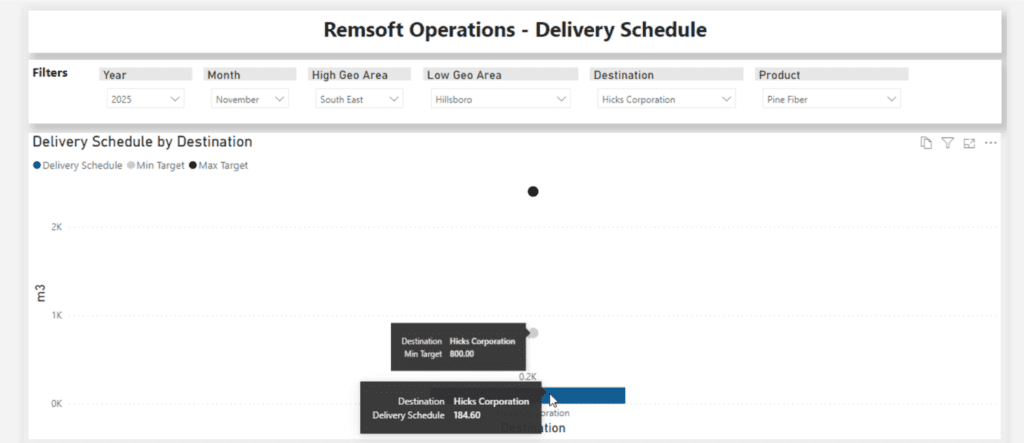
While this should be a simple thing to do, unfortunately, it often isn’t. With data stored across numerous systems or multiple spreadsheets, even relatively minor adjustments like these can be daunting and complicated. Especially when you consider how many spreadsheets contain several crosstab formulas that are frequently only understand by the workbook’s author.
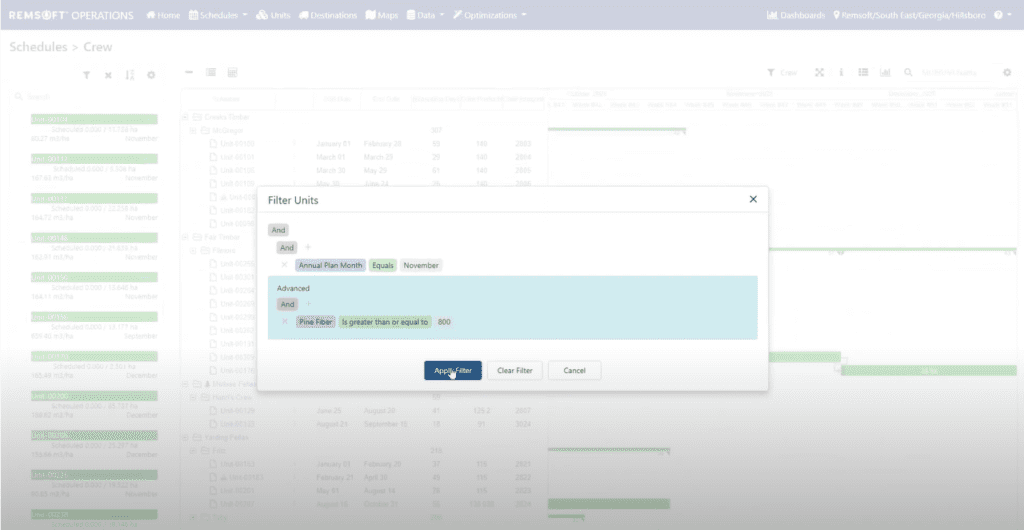
However, working on a cloud-based, unified platform like Remsoft Operations, planners have access to everything they need to make any changes. The intuitive design makes it easy to understand how to complete each task, even if they’re not familiar with a specific region. Operational and delivery plans can be quickly updated, and then further analysed and validated through various graphs and reports. And in many cases, it’s just a few steps: adjust the destination’s product targets, validate planned wood volumes, identify additional product volume availability, and then assign a harvesting crew to the new unit.
With planning aligned across your organization, you can always make updates and adjustments when they are needed to keep your plans flexible and responsive and your customers satisfied.
What’s Your Planning Challenge?
With adaptive and collaborative planning supported by Remsoft Operations, you can respond to any real-world challenge that comes your way.
If you’d like to learn more about how we support dynamic forest-to-mill planning, you can view our new use case video series to see our cloud-based Remsoft Operations platform in action.
LEARN MORE:
- Take a closer look at how Remsoft Operations drives value by booking a demo today.
- Watch our On Demand webinar, The Story of a Block, to look at the lifecycle of a block and how Remsoft Operations can help to maximize potential at every decision point.